REU PROJECT (2024)
Clay 3D Printing
Hybrid Workflows Track
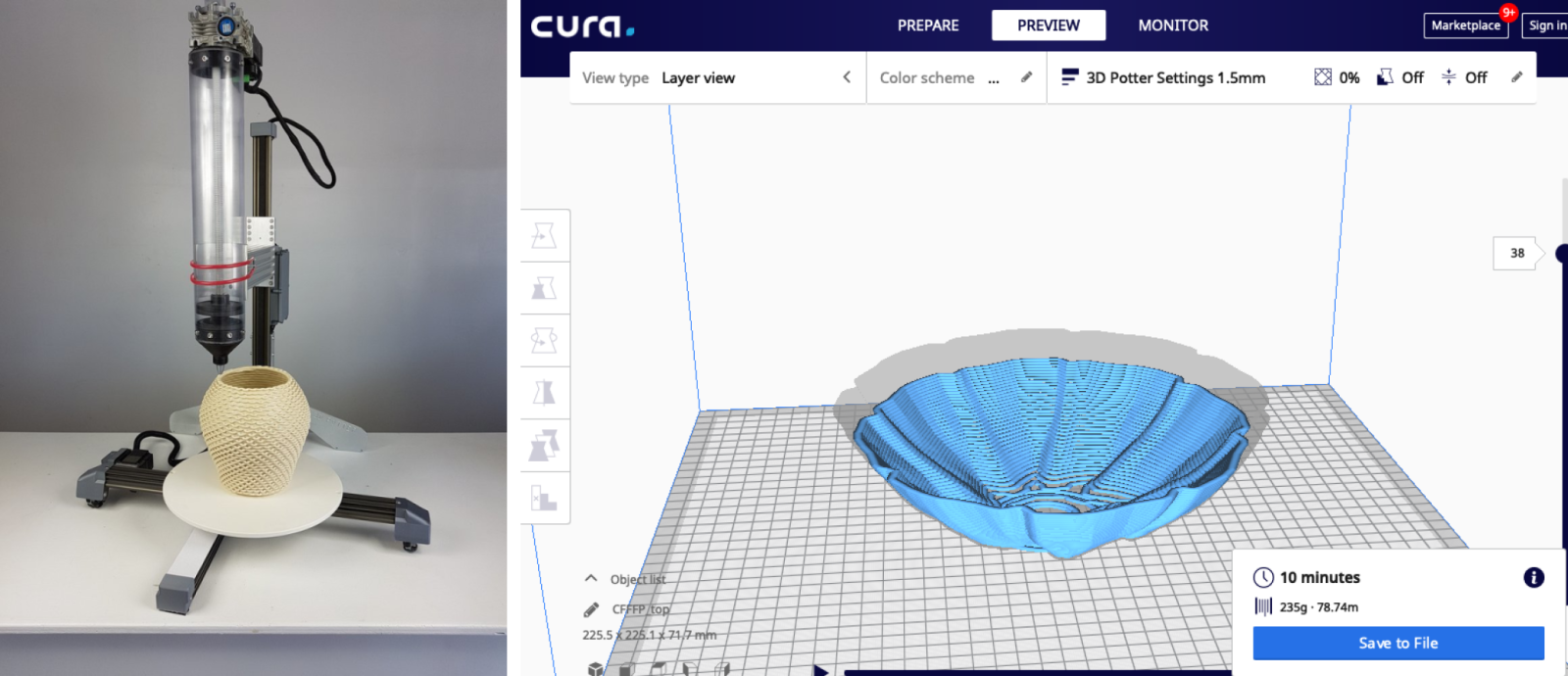
Description
Clay 3D printing uses a continuous deposition technique to extrude and fuse clay coils into clay forms which can be generalized to other paste-based materials including concrete, food, and silicone printing; however, this technique is limited in the geometries it can support (to prevent rupture during the ceramic firing process). Interactive CAM algorithms could allow a user to recover, repair, and reuse elements of a clay form and yield a more robust, sustainable, and expressive clay printing workflow.
Leveraging established techniques from the ceramics community, this multi-researcher project will use computational and electromechanical methods to develop interactive clay 3D printing techniques.
Project goals would examine modular G-Code decomposition, specifically:
- Designing a slicing algorithm to convert 3D models (STLs) into machine instructions for the PotterBot. The algorithm will decompose complex 3D shapes into components that can be fused using traditional hand-building techniques. This would allow the slicing algorithm to support human intervention to repair and reform failed geometries (e.g., adding support structures).
- Integrating the slicing routine into a user interface and evaluate the hybrid clay building workflow in a user study.
- Exploring extruder design including retrofitting a mechanical tube-cutting and scoring mechanism to the extruder assembly of the PotterBot and develop a sensing circuit to characterize the water content and, by proxy, material behaviors of the clay.
- Designing a human-in-the-loop system that supports direct manipulation of the extruder.
This work will result in open-source software and hardware to the larger PotterBot community and a gallery of inspirational clay forms and tutorials to further elevate clay as a prototyping material.
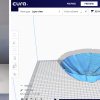